Understanding the loler test: Ensuring Safety and Compliance in the Home & Garden and Pest Control Industries
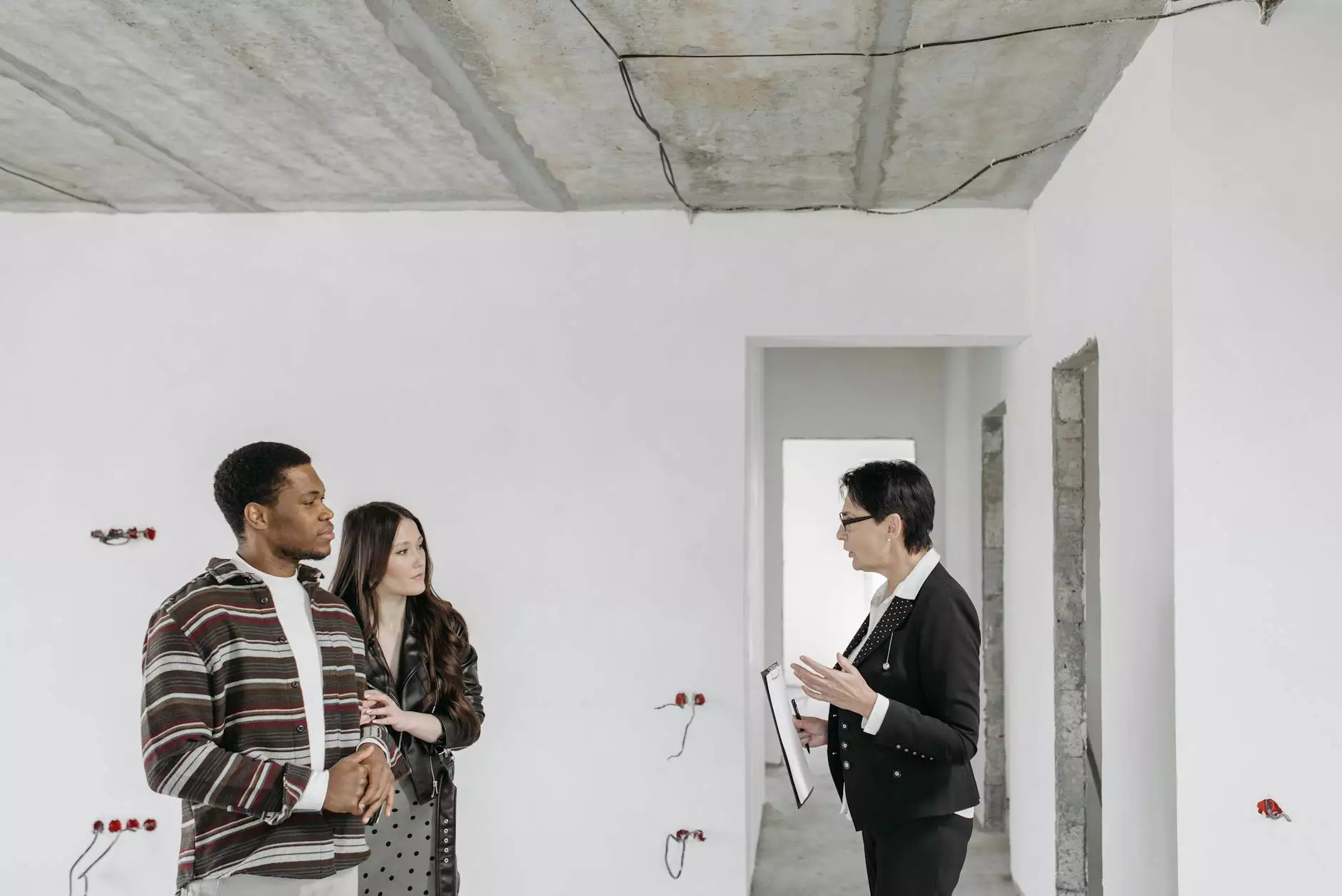
In the fast-evolving landscape of business operations within the Home & Garden, Gardeners, and Pest Control sectors, adherence to safety standards is paramount. Among these standards, the loler test plays a crucial role in safeguarding workers, clients, and the environment while maintaining legal compliance. This comprehensive guide explores the significance, process, and benefits of the loler test, and how businesses such as SafePlant UK provide expert services to ensure that your operations are safe, efficient, and compliant.
What is the loler test? An Essential Overview
The loler test is an abbreviation for the Lifting Operations and Lifting Equipment Regulations 1998. These regulations mandate that all lifting equipment used in workplaces must be regularly inspected and maintained to minimise the risk of accidents. While primarily associated with lifting gear, the loler test encompasses safety testing and compliance for a wide range of equipment in various industries, including those involved in Home & Garden services, gardening tools, and pest control machinery.
Why the loler test is Crucial for Your Business
Implementing regular loler tests offers numerous benefits that directly impact your company's safety standards, legal compliance, and reputation:
- Legal Compliance: Adhering to UK safety laws to avoid fines, penalties, or work restrictions.
- Workplace Safety: Preventing accidents caused by malfunctioning or damaged equipment.
- Operational Efficiency: Ensuring equipment functions correctly, reducing downtime and breakdowns.
- Protecting Staff and Clients: Prioritising safety creates a trusted environment for clients and a safe workplace for employees.
- Insurance and Liability: Maintaining compliance can streamline insurance claims and reduce liabilities.
The Scope of Equipment Covered by the loler test
The loler test applies to a broad spectrum of equipment prevalent in the Home & Garden and Gardeners sectors, such as:
- Electric-powered lawnmowers and garden machinery
- Chainsaws and pruning equipment
- Pest control devices including foggers, traps, and sprayers
- Lifting equipment used for moving heavy materials or garden structures
- Portable electrical tools and extension leads
- Suspended or mobile scaffolding used in garden structures or maintenance
The Process of Conducting a loler test
Conducting a loler test is a meticulous process involving several critical steps to ensure equipment safety and compliance:
- Visual Inspection: A thorough examination of the equipment's physical condition, looking for signs of wear, damage, or corrosion.
- Mechanical Inspection: Testing moving parts and structural integrity.
- Operational Testing: Confirming the correct functioning of safety features and operational mechanisms.
- Electrical Testing: Checking wiring, insulation, grounding, and circuit integrity, especially for electrical equipment.
- Recording Results: Documenting the inspection findings, noting any repairs needed, and issuing a test certificate if safe.
- Maintenance and Repairs: Addressing any issues uncovered during testing to restore equipment to optimal safety standards.
Frequency and Legal Requirements for loler testing
The frequency of loler tests depends on the type of equipment, usage intensity, environment, and manufacturer recommendations. Typically:
- Electrical equipment used daily or in high-risk environments should be tested at least every 6 to 12 months.
- Less frequently used machinery may require testing every 2 to 3 years.
UK law mandates that all lifting and electrical equipment must undergo loler testing by a qualified person and be maintained under a documented regime. Failing to comply can lead to significant penalties, legal actions, and increased risk of accidents.
How SafePlant UK Supports Your Business with loler test Services
SafePlant UK delivers expert loler test services tailored to the unique needs of the Home & Garden, Gardeners, and Pest Control companies. Our certified inspectors ensure:
- Comprehensive safety assessments of your equipment
- Preparation and certification documentation for legal compliance
- Timely scheduling of periodic tests to avoid lapses
- Maintenance advice and repair services to address issues identified during testing
- Consultation for best practices in equipment safety and compliance management
The Impact of Proper Equipment Testing on Your Business
Regular loler test not only ensures compliance but also enhances your business operations and reputation. It demonstrates to clients and staff that safety is a top priority. Furthermore, it minimizes downtime, reduces unexpected repair costs, and mitigates legal risks.
Best Practices for Maintaining Equipment Safety Post-Testing
Conducting the loler test is just the beginning. Implementing ongoing maintenance routines is crucial for sustained safety:
- Perform routine visual inspections before each use
- Keep detailed maintenance logs and inspection records
- Follow manufacturer guidelines for servicing and replacement
- Ensure all staff are trained in proper handling and safety procedures
- Schedule periodic professional inspections as mandated by law and industry standards
Understanding the Legal Framework Surrounding the loler test
The legal landscape in the UK for equipment safety revolves around the Laws of the loler test. The key regulations include:
- Health and Safety at Work Act 1974
- Management of Health and Safety at Work Regulations 1999
- Provision and Use of Work Equipment Regulations 1998 (PUWER)
- Fire Safety and Equipment Regulations
These laws collectively require employers and business owners to ensure that all work equipment is maintained in a safe condition through regular testing, inspection, and proper documentation, with the loler test being central to these requirements.
Common Challenges and Solutions in Equipment Compliance
Many businesses face hurdles such as scheduling regular inspections, maintaining accurate records, and ensuring staff are trained. The solution lies in partnering with experienced professionals like SafePlant UK, who make compliance seamless and stress-free.
Conclusion: The Power of Proactive Equipment Safety Management
Investing in regular loler test services is a proactive step that safeguards your business, enhances operational efficiency, and demonstrates a strong commitment to safety and legal compliance. Companies operating within the Home & Garden, Gardeners, and Pest Control sectors must understand the importance of this vital safety measure and work with trusted experts to implement it effectively.
Remember, safety is an ongoing process, not a one-time check. Regular testing, maintenance, and staff training are essential components of a sustainable, compliant, and reputable business. Trust SafePlant UK to support you in maintaining the highest safety standards through expert loler test services and ongoing safety management.
Take Action Today
Ensure your business adheres to all legal requirements and promotes a safe working environment by booking your loler test with the experts. Contact SafePlant UK today and get peace of mind knowing your equipment meets all safety standards.