Understanding SAE Thread Dimensions: A Comprehensive Guide
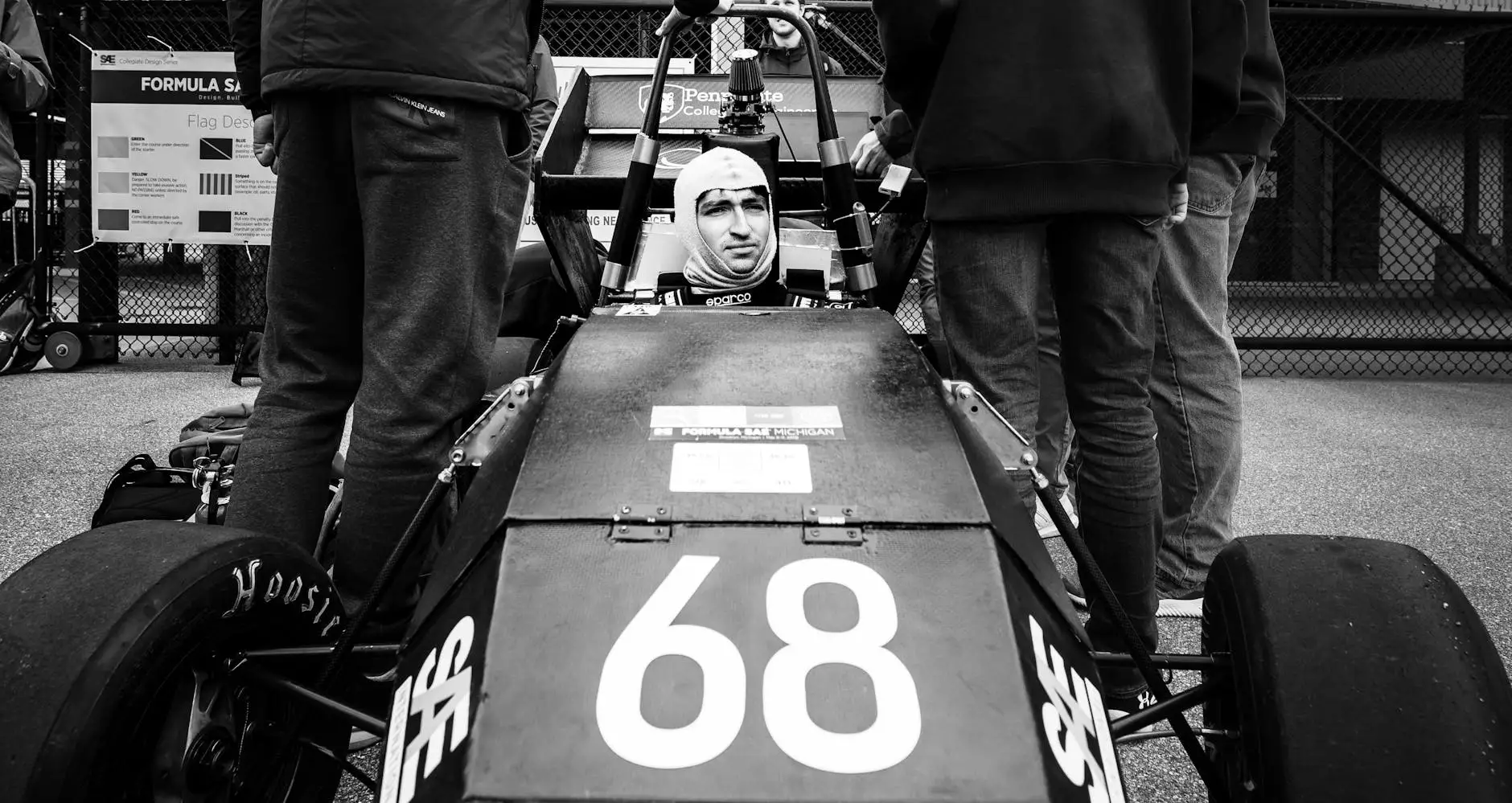
SAE thread dimensions play a crucial role in the manufacturing and engineering sectors, particularly in automotive and industrial applications. The Society of Automotive Engineers (SAE) has established a set of standards that ensure consistency and compatibility among threaded components. This article delves into the intricacies of SAE thread dimensions, their specifications, and their significance in fostering effective communication and interoperability in mechanical designs.
What are SAE Threads?
SAE threads refer to the standardized specifications for screw threads as defined by the Society of Automotive Engineers. These standards are essential for manufacturers, engineers, and designers who work with threaded fasteners in various applications. Understanding these thread dimensions helps ensure that components fit perfectly, function as intended, and enhance the overall quality of the product.
History and Development of SAE Standards
The standards established by the SAE have evolved over the years, responding to changes in technology and industry needs. Initially, these standards were created to unify the design and manufacturing processes among automotive and aerospace industries that relied heavily on threaded fasteners. Today, the significance of these standards extends beyond automotive to multiple sectors, including construction, machinery, and consumer products.
Importance of SAE Thread Dimensions
Understanding SAE thread dimensions is vital for several reasons:
- Interoperability: Consistent dimensions ensure that components from different manufacturers can be used interchangeably.
- Safety: Properly sized threads contribute to the structural integrity of assemblies, thereby enhancing safety.
- Efficiency: Accurate measurements streamline the manufacturing process and reduce the need for adjustments and modifications.
- Quality Control: Standard dimensions simplify quality checks and compliance with industry regulations.
SAE Thread Specifications
SAE threads are categorized primarily into two types: Unified National Coarse (UNC) and Unified National Fine (UNF). Each type has specific thread dimensions, including pitch, diameter, and angle, which influence their application and performance.
Thread Dimensions Breakdown
The following are the critical components of thread dimensions:
- Major Diameter: This is the largest diameter of the thread. It is crucial for fitting applications where space and load-bearing capacity are factors.
- Minor Diameter: The smallest diameter of the thread, important for determining the core strength of the fastener.
- Pitch: The distance between threads measured parallel to the axis. It plays a significant role in the grip and holding capacity of the fastener.
- Thread Angle: The angle between the flanks of the thread, usually expressed in degrees. Different angles can influence the engagement and load distribution of the threads.
SAE Thread Dimension Chart
Here is a helpful chart of SAE thread dimensions for UNC and UNF series:
Thread Size (inches)Major Diameter (inches)Pitch (inches)Threads Per InchMinor Diameter (inches)1/4-20 UNC0.25000.0500200.19001/2-13 UNC0.50000.0769130.44203/8-16 UNF0.37500.0625160.30705/16-18 UNC0.31250.0556180.2500How to Measure SAE Thread Dimensions
Accurate measurement of SAE thread dimensions is crucial in ensuring compatibility and performance in threaded applications. Here are the recommended tools and methods:
Tools Needed
- Caliper: A digital or manual caliper can provide precise measurements of the major and minor diameters.
- Thread Pitch Gauge: This tool measures the pitch of the threads accurately.
- Tapered Plug Gage: Used to check the fit of the threads in designed holes.
Measurement Steps
- Measure the Major Diameter: Use the caliper to measure the diameter at the top of the thread.
- Measure the Minor Diameter: Measure the diameter at the bottom of the thread using the caliper.
- Determine the Pitch: Use a thread pitch gauge to identify the number of threads per inch or overall pitch distance.
- Check the Thread Angle: A protractor can help verify the thread angle, ensuring it matches SAE specifications.
Applications of SAE Threads
SAE thread dimensions are utilized in numerous applications, contributing to the effectiveness and safety of products. Here are some of the most common applications:
- Automotive Manufacturing: SAE threads are widely used in vehicle assembly, where consistent strength and reliability are essential.
- Aerospace Engineering: The aerospace sector often relies on SAE threads due to their precision and uniformity under high-stress conditions.
- Industrial Equipment: Machinery relies on SAE-threaded components to ensure smooth operation and longevity.
- Construction: Many construction projects utilize SAE threaded fasteners to ensure structural integrity.
Choosing the Right SAE Threads for Your Projects
Selecting the correct SAE thread dimensions for your project is pivotal. Consider the following factors:
Load Requirements
Assess the load conditions that the bolts and screws will need to endure. SAE threads come in different strengths and dimensions, so it is essential to choose those that can handle the intended load without failure.
Material Compatibility
Different materials may require specific thread types. For instance, softer materials may require finer threads to penetrate without stripping.
Environmental Conditions
Consider the environment where the components will be used. Corrosive or high-temperature settings might necessitate special coatings or material selections to enhance resistance.
Resources and Further Reading
For those seeking to deepen their understanding of SAE thread dimensions and the impact of these specifications on various applications, numerous resources are available:
- SAE International: Visit the official website for updated standards and publications related to thread specifications.
- Technical Manuals: Many manufacturers provide manuals that detail the specifications of their products and the corresponding SAE standards.
- Online Courses: Several platforms offer courses focused on engineering standards that cover SAE threads in depth.
Conclusion
In conclusion, understanding SAE thread dimensions is indispensable for anyone involved in engineering, manufacturing, and design. As we have explored, these standardized specifications not only ensure compatibility and safety but also significantly enhance the efficiency of production processes. The emphasis on quality control, measurement accuracy, and appropriate application selection cannot be overstated. For those interested in sourcing high-quality fittings and related components, refer to fitsch.cn for a comprehensive selection tailored to your needs.